As a result of Anders Grönlund’s ground-breaking research, Norra Timber’s Kåge and Sävar sawmills are today considered among the most modern facilities in the entire world – with large CT scanners that process 1,750 logs per hour.
“Thanks to scanning technology we can get between five and ten percent more out of every log”, says Anders Grönlund.
Anders Grönlund, together with his colleague Owe Lindgren, a Professor of Non-Destructive Testing, could often be seen running around Skellefteå Hospital during the late 1980s and early 1990s carrying logs which they would X-ray with a CT scanner – the same equipment that would be used to X-ray people in the morning and logs in the afternoon.
“At that time, most sawmill managers didn’t even think about ways to extract more from each log. They just tried to reduce the number of people working at the sawmills, as employing staff was expensive in Sweden and so they tried to cut costs. To me it felt wrong, because raw materials account for about 70 percent of a sawmill’s costs, so I started thinking about the problem in other ways”, says Anders Grönlund.
He realized that if you could somehow know what a particular log looked like from the inside, you could adjust the sawing process accordingly. And thus his timber X-ray idea was invented.
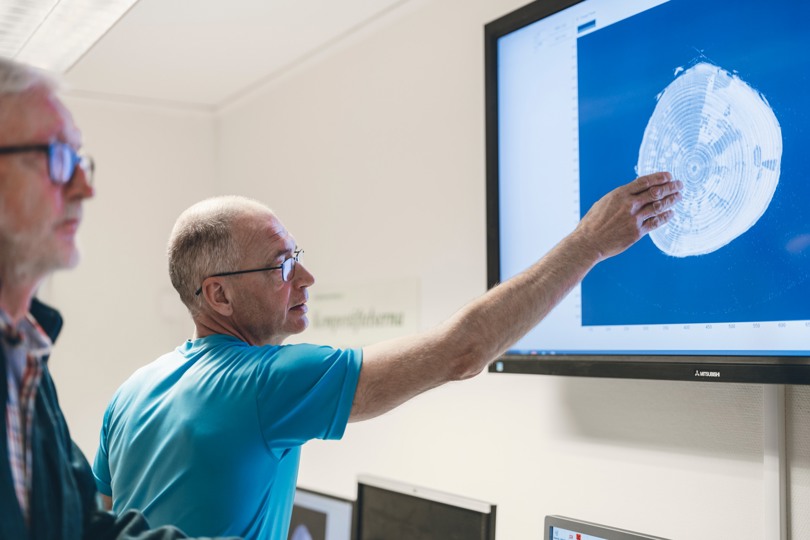
Developed a ‘log bank’
After X-raying logs at the hospital for a few years, the pair finally got their own tomograph in 1992. Work then began developing a ‘log bank’, in which 200 firs and 200 pines from various parts of Sweden were scanned on campus at Skellefteå University.
“The log bank became a great example of what a forest can look like – and it is still used today. We X-rayed every centimeter of each log, which at the time took several hours per log. Today at Kåge and Sävar it takes just one and a half seconds. Handling large logs in a lab was quite complicated and heavy back then – but it was fun too”, says Anders Grönlund, laughing.
He adds:
“We were the first in the world to do it and are still the world leader in X-raying timber to this day”.
Their work on scanning logs was also picked up by the BBC, who came to Skellefteå and published a detailed report of their research.
“Among other things they filmed us when we carried a log on a stretcher into the hospital”, says Anders Grönlund with a smile.
Took scanning technology to the next level
In the beginning of the 1990s, Anders Grönlund, together with Johan Oja, who was then a PhD student and Stig Grundberg, the then Head of Sävar Sawmill, also participated in an EU project which eventually led them to make contact with Italian Federico Giudiceandrea. He took the scanner technology even further and succeeded in developing a fast scanner – for which he received the prestigious Wallenberg Prize in 2016. The prize, which was presented in Stockholm by His Majesty the King, is considered the forestry industry’s Nobel Prize, and is worth SEK 2 million.
“It was myself and Johan Oja at Norra Skog who recommended the eventual prize winner. The award was really a feather in the hat for the entire development process”, says Anders Grönlund.
Anders Grönlund’s work at LTU (Luleå University of Technology) in Skellefteå has contributed to as many as thirty technology doctorates and a number of technology licentiates over the years, including the academic journeys of Johan Oja and Jens Flodin at Norra Skog.
“Jens Flodin, for example, has worked with the concept that every log is a unique individual, and that you can identify a log just as you can identify a person with the help of DNA and fingerprints”, says Anders Grönlund.
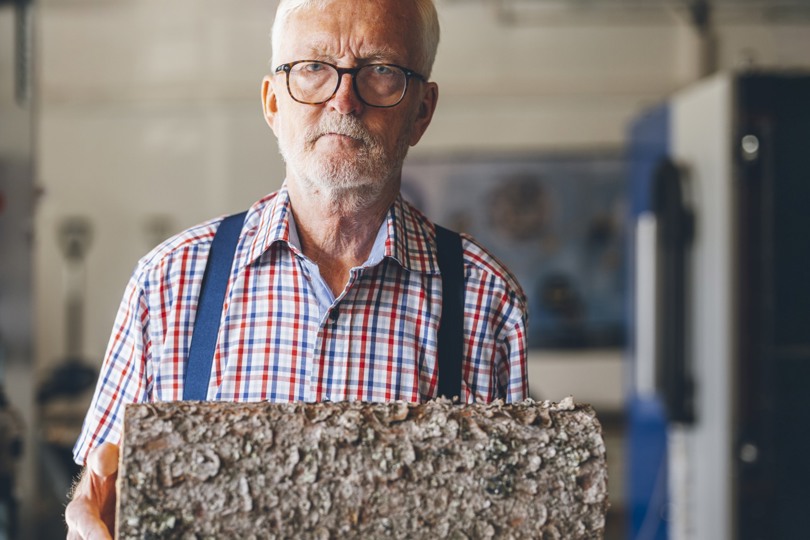
Branches end up where they do the least damage
At Kåge Sawmill each log is X-rayed and then sorted into different piles. Once the log arrives at the saw line (which can be up to a month afterwards), the saw instantly recognizes the log and can use its measurements to guide the log correctly while sawing it. The scanned log is then turned into exactly the right position in the saw so that any branches end up where they do the least amount of damage.
“You could say we are able to ‘hide’ the branches. It may sound a little suspicious, but if you are going to make, for example, a window frame, it doesn’t matter if a knot is located against the side of the wall. It is not visible and does not affect the product. Taking this approach means the value of each log is increased”, says Anders Grönlund.
He adds:
“The sawmill industry has been considered low-tech for a long time now, but this development, which is based on advanced data, is really high-tech. The CT scanners at the sawmills in Sävar and Kåge are state-of-the-art. There’s nothing out there that compares to them”.
Anders Grönlund is now retired and lives with his wife Ulla in Ersmark outside Skellefteå. They live on a farm that has belonged to Anders’ family for generations, from where he still keeps up-to-date with technological developments in the timber industry.
“We live just six kilometers from Kåge Sawmill, where Norra Timber is now installing its second CT scanner. It feels like a second home to me”, concludes Anders Grönlund.