An important benefit of the company’s state-of-the-art scanning process is improved traceability. Now each log can be identified individually, just as a person can be identified by their DNA or fingerprint.
“We can now match exactly the right log to the right customer or the right product. By doing so we reduce the piles of sawn material that no one wants to buy”, says Jens Flodin, who works as a Production Optimizer at Norra Timber.
In 2008, Jens wrote a thesis on traceability that was based on the premise that timber is a biological product, and that each log is a unique individual, just like human beings.
“There were already traceability projects in operation, for example where a partial flow was followed through the entire production using so called RFID tags, which stands for radio-frequency identification – a technology for transmitting information from a distance using transponders and RFID readers.
“Another way to obtain production chain data is via traditional trial sawing, but this method involves a lot of manual work. Every log needs to be marked, and you have to keep track of the order in which logs arrive and handwrite numbers on the planks as they are sorted in the grading mill.
But now our computer tomograph, which is also known as a CT scanner, makes our work significantly easier on a larger part of our production flow. In addition it does not require anywhere near as much administration”, says Jens.
Thanks to the improved traceability the CT scanner provides it will eventually be possible to follow a log from its felling site to a finished product. Another major benefit is that you can also identify what each log is best suited for.
“Our customers have different requirements. Some may, for example, have specific expectations for a certain percentage of heartwood. If you then saw logs which have not been scanned and pre-sorted you can be left with a substantial pile of residue that does not meet the requirements for a customer’s products. It could also be that they have been sawn to odd dimensions or dried to a certain degree so that it is difficult to produce the right products and get paid for them”, explains Jens.
If instead you could scan the log and give it a unique ‘fingerprint’, you can then identify which end products the customer wants, and exactly which logs should be used to make them.
“This minimizes the waste that no one wants – which is a massive benefit”, says Jens.
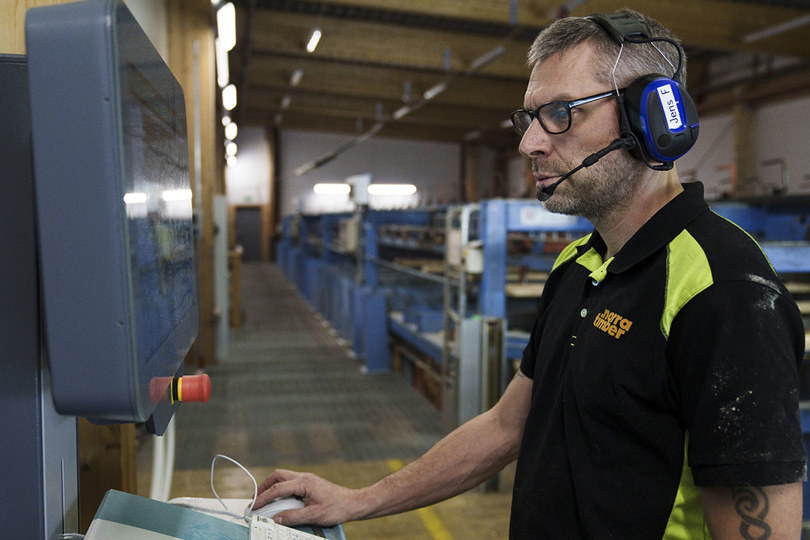
Another advantage of the CT scanner is that it can accurately determine how much of the log is bark and how much is wood.
“If you know that then there’s an immediate financial gain, because we all like to know down to the millimeter how much bark and wood there is”, says Jens.
Sävar Sawmill also has a similar saw line to Kåge, and Jens Flodin believes Norra Timber is unique in the world for operating such a high level of technology.
“There are about ten similar facilities around the world – and two of them are in Norra Timber sawmills. We are at the very forefront of development”, says Jens, who adds:
“This is the way to prosper in the long term. We must be able to use logs, which have grown slowly in our forests for a long time, in the most optimal way possible. It’s the key to our success in the future.”